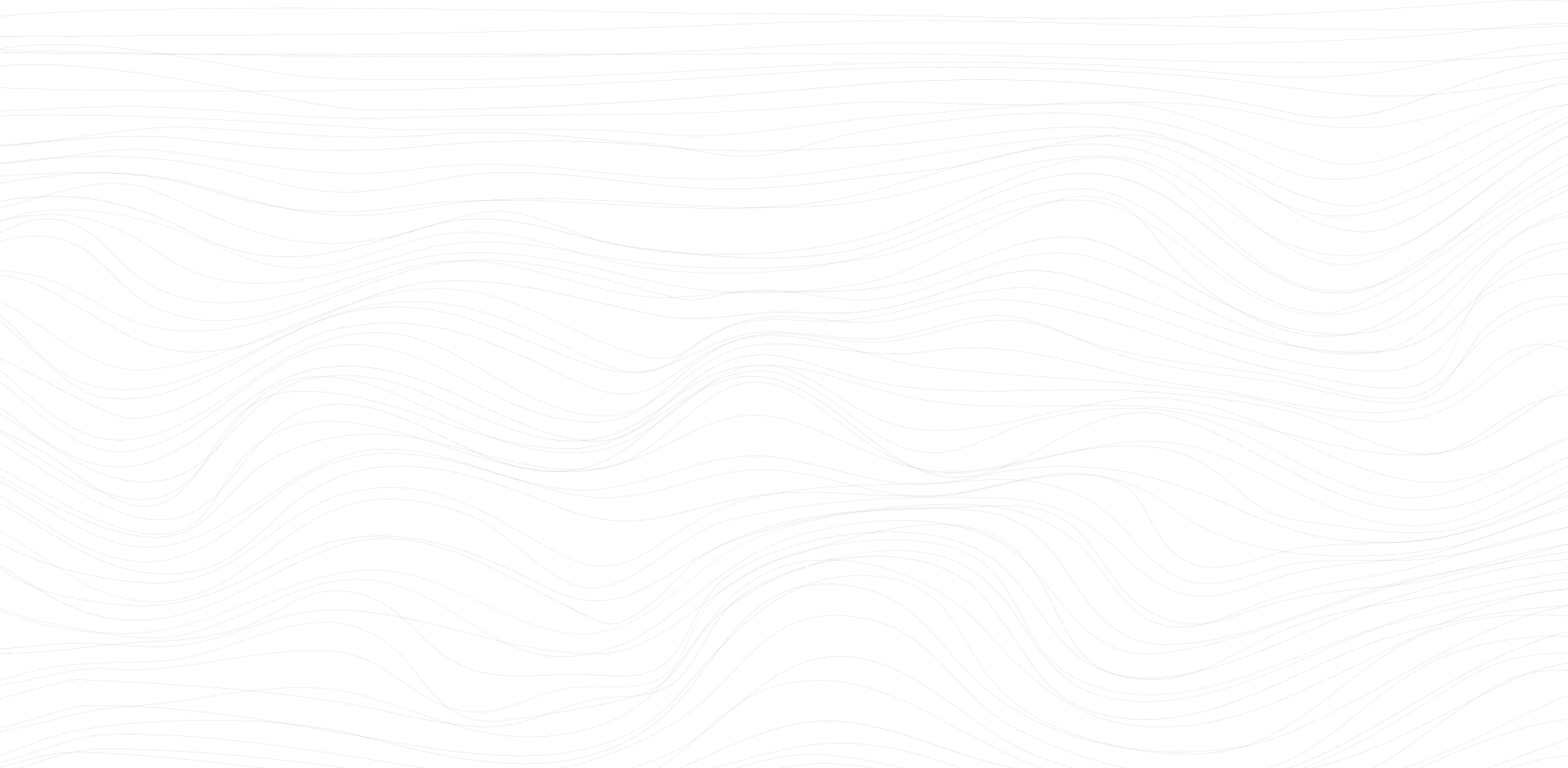
Valve Actuator is a mechanism that used for move or control the valve. It’s a component that produce forces when an electrical, pneumatic, or hydraulic input is supplied to the actuating system. It can move the valve based on commands so that the valve can open, shut, or regulate fluid flow as desired. The mechanism can be activated by using a mechanical arm that is usually driven by an electric motor, which is controlled by a programmed automatic control media including a microcontroller.
There are 2 working conjunction component parts of the actuator, valve body & valve pilot. There’s also a several parts of the components inside the mechanism device itself such as bonnet, engine valve spring or diaphragm, yoke, clutch block, drive indicator, upper spindle, vent plug, & adjusting crew.
In terms of functionality, the valve actuator has a variety of important functions to enable the operation of its device. It can be used for moving the valve, controlling the fluid flow, maintaining the precision and the accuracy, provide the responsiveness, & optimize the system’s safety. There are several types of the actuators that commonly equipped for the valves.
1. Diaphragm Actuator
This type of valve actuator is used air pressure from within the diaphragm housing in order to push the actuator rod down. This process is known as “direct-acting,” which results in air compression. It usually used for control valve to regulate the fluid flows in order to adjust pressure, temperature, and flow rate.
2. High Pressure Actuator
Similar to diaphragm type, it’s also used air pressure as well. But on this type of mechanism, it’s designed to work with high pressure. It’s generally used for industrial applications that required high pressure and faster movement. For example, higher pressure application can make it much difficult to operate the mechanism, so it has to required high pressure actuator to achieve the torque performance.
3. Pneumatic Actuator
This piston shaped mechanism that is used to move various mechanical components, such as valves, conveyors, and other equipment. It provides enough force power to control the movement of these components in various industrial applications. One such case for example, it can be used for mining industry where pneumatic actuator drive the valve to regulate the pressure within the nozzle on the stone washing line.
4. Electric Actuator
A mechanism that is used electric as a power source to move the valve. It can enhance rotational movement which is converted into linear motion by using mechanism, i.e., screws or gears. For the valve operation, it able to facilitate the valve to control the flow of fluids within pipeline.
5. Electro-Hydraulic Actuator
Combining the electromechanical and hydraulic components, it used an electric force to drive a hydraulic pump then push hydraulic fluid in order to move the valve. For purpose, it aims to replace hydraulic system with standalone actuator operated solely by electrical power. Aircraft control surface required the precise control over motion, in order to operate the application, electro-hydraulic actuator provide proportional control of force to the automotive application, this would made the operation much smoothly.
For the advantages of the valve actuator, it has a responsiveness, precision control, more durable, non-dependent on external power sources, & able to withstand the heavy loads. But on its disadvantages, it much more costly, require more maintenance, require electric force, complex to control, & much heavier by design.
The vital role of actuator in the industrial sectors is crucial for assisted the valve to operate for the various industrial applications such as oil and gas, petrochemical, energy, and other sectors. It enable the operation process for the valve and it makes much easier for every sectors to achieve the efficiency.
References :